Hey guys, I've been getting some PM's about this so while I am NOT a fiberglass expert I figured I could answer here what I do know.
here are the questions:
1. Is this method strong? YES pound for pound it's is MUCH stronger than glass alone in bend and twist resistance.
I think the foam is able to spread what would be localized stresses through out a much greater area? (one of the engineer guy's can prob explain this much better than me)
2. Putting filler on the glass adds alot of weight? NO, There is no gel coat layer so it's kind of a push. I have a 1.75lb qt can of filler and have used about half the can on three panels, If you also take into account that 50% of the filler gets sanded off and lands on the floor it's not much weight ant all per panel.
3. Will it hold up to high speeds or is it flimsy? This method isn't new, "I think" it was invented by an airplane builder in the 70"s (check out the long EZ and many others) It's also used by boat, car, surfboard, etc....builders.
4. Why can't I use the cheap poly resin found in my local hardware/auto parts store? You can BUT, poly resin will eat the blue, pink, yellow (cheap) foam and leave a gooey nasty mess! (You don't want to know how I found this out

) You need to use urethane foam with poly resin.
Also Poly resin is not a glue so to speak, It bonds by a chemical means only if its all done at one time otherwise it is just a mechanical bond and may de-laminate if it's done wrong.
5. Can I peel out the foam? YES, however glassing the foam on BOTH sides is why it's strong in bend and twist, once the foam is out it will take many many layers of mat turned 45 deg to the previous layer to even get close to the same strength.
There are many books on this and because it's the way that works for me doesn't mean it's the absolute correct way!
Warren is right about the peel ply but I've also found wax paper to work very well, here is a pic of a side pod with the wax paper just removed, It's very smooth and will require a very light surface sand and light filler (just like they do when they make a custom motorcycle fuel tank.)
PooK
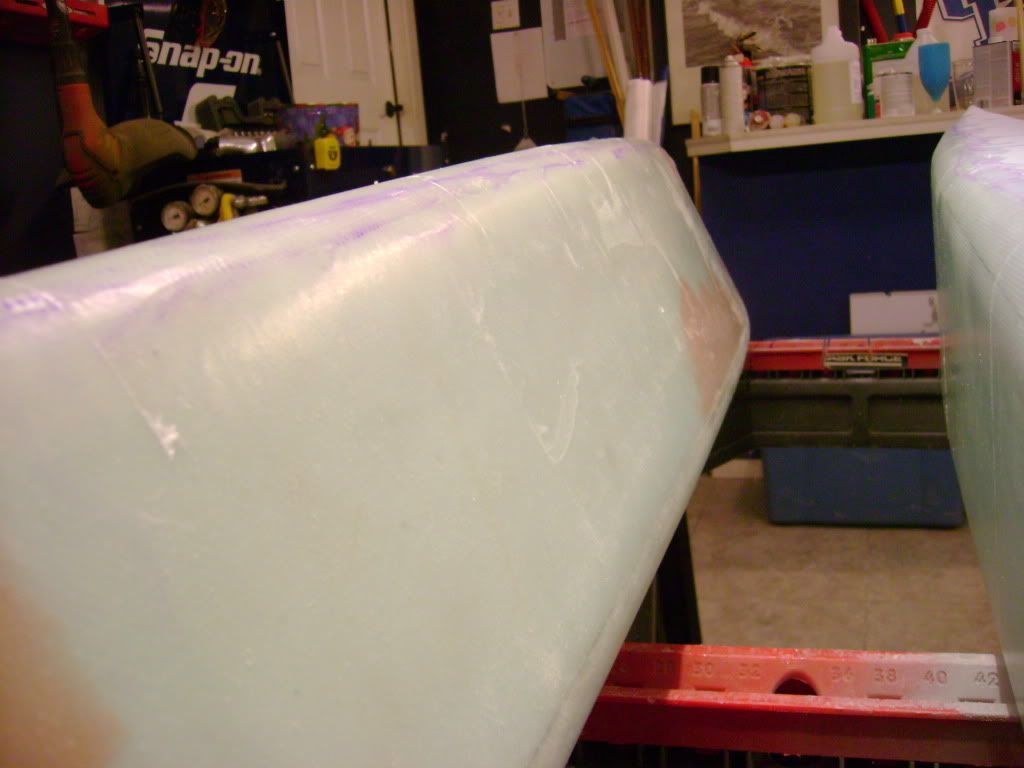